SherSor/iStock/GettyImages
Every cent counts in tough economic times, and reusing cooking oil for your family's favorite fried, seared or browned chicken recipe is one way to save a bit on your grocery bills. This practice is not without risk, however. If you're a meticulous mom who takes the time to handle food properly, you can do this safely. Otherwise, safety concerns might be reason enough to keep your shelves stocked with fresh cooking oils.
Start With a High-Temperature Oil
Many chefs swear by reusing oil, particularly for seasoned dishes such as fried chicken, as they say it adds character and flavor to their meals. In general, this practice is perfectly safe, but it depends on what sort of oil you use and how you plan to prepare your chicken. All oils have a property called the smoke point, a temperature at which an oil begins to burn and emit smoke. Not only will this make your chicken taste unpleasant, but it could potentially be dangerous. Certain oils have higher smoke points than others, and all oils will have a lower smoke point after you heat them once. Therefore, it's usually not a good idea to reuse oils when searing or frying chicken at high temperatures.
Smoke Point Options
Most vegetable oils have a smoke point of between 400 and 450 degrees Fahrenheit, well above the optimal frying temperature of 375 F. Smoke points will depend on the quality of the oil and how it was processed, but grapeseed, peanut, canola, safflower and soybean oils have some of the higher smoke points of common cooking oils. Processed olive oil also has a high smoke point, but extra virgin olive oil has a lower smoke point, so you shouldn't use it to fry chicken, even when fresh. Once you heat an oil, its smoke point can drop by as much as 100 degrees, depending on how long it was heated, how it was stored and how much foreign matter got into the oil.
Safe Re-Use
If you want to reuse oil, treating it and storing it properly is essential to keeping the smoke point high enough to safely cook chicken. When cooking, you should use a thermometer to ensure heating is not exceeding proper frying temperatures. Once you've cooked, let the oil cool, then strain it through a cheesecloth or coffee filter to remove food particles. You then should store the oil in an airtight container in the refrigerator, shielding it from exposure to heat and excess light. When using the oil to cook chicken, you can mix it with fresh oil to help normalize the smoke point, but make sure it's the same type of oil. Mixing different oils together also can lower their smoke points.
Use Your Judgement
Improperly reusing oil can present several forms of danger. For one, after an oil heats past its smoke point, it can reach a flash point, at which point it will burst into flames. When it reaches its smoke point, oil also changes its composition, developing free radical compounds that could possibly cause cancer. Your best bet is to give the oil a sniff test before you trust it with your chicken. If it smells fine when cold, heat up a small quantity in your skillet. If you don't detect any "off" smells, it's not rancid and should be safe to use.
Related Articles
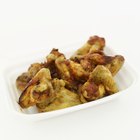
What Kind of Oil Should I Use to ...
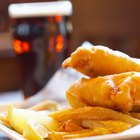
What Type of Oil Can I Use to Deep Fry ...
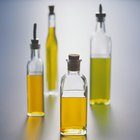
Cooking Oils With Low Smell

How to Use Oil in a Nonstick Pan
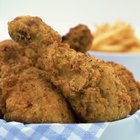
How Much Oil in a Pan to Fry Chicken ...
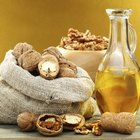
Substitutes for Walnut Oil
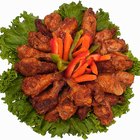
How to Cook Fried Drummettes
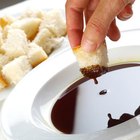
The Shelf Life of Pumpkin Seed Oil

How to Deep-Fry a Chicken in Minutes
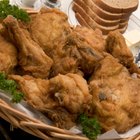
How to Par-Cook Chicken Before Frying
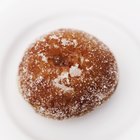
Can Doughnuts Be Deep Fried in Olive ...
How Long Can You Keep and Reuse Peanut ...
Cooking With Camellia Oil
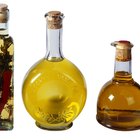
What Kind of Oil Do I Use to Cook a ...
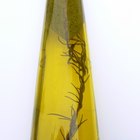
Which Olive Oil Is Best to Fry With?
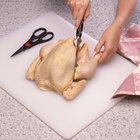
Can You Cold Smoke Chicken?
Can You Cook Frozen Chicken?
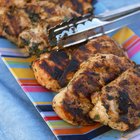
The Differences Between Baking, ...
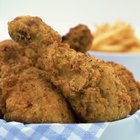
Can I Make Fried Chicken With Butter ...
How to Make Homemade Tortilla Chips
References
Writer Bio
Michael Baker has worked as a full-time journalist since 2002 and currently serves as editor for several travel-industry trade publications in New York. He previously was a business reporter for "The Press of Atlantic City" in New Jersey and "The [Brazoria County] Facts" in Freeport, Texas. Baker holds a Master of Science in journalism from Quinnipiac University in Hamden, Conn.