Introduction
To be made into fabric, wool undergoes several processes. The fleece is sheared from the sheep, scoured, carded, combed and spun into yarn. The yarn is then woven on a loom to create wool fabric. There are two types of wool yarn that make different fabrics: woolen and worsted.
Shearing
Sheep are sheared once a year by professionals who shear the whole fleece in one piece. The fleece is moved to a wool table, which has slats spaced apart to allow shorter wool and debris to fall underneath. Twigs, leaves and undesirable parts of the fleece are removed by hand, and the remaining fleece is folded and rolled.
Classing
The fleece is examined and graded according to the length, diameter, strength, crimp and color of its individual fibers. Finer wool is used to make worsted fabric for suits and other garments, while coarser wool is made into woolen fabric for coats, jackets and rugs. Fleeces of the same grade are mechanically pressed into bales and stored ready for transportation.
Scouring
Raw fleeces contain lanolin, which makes them greasy, and they will still hold vegetable matter from the fields. Scouring cleans the wool and removes the lanolin by raking it in baths of hot water, detergent and alkali. The wool is rinsed, squeezed by rollers and dried.
Blending
To make wool from multiple fleeces more regular in fiber size and color, the clean wool from different batches is mechanically mixed.
Carding
The mixed and washed wool consists of tufts of tangled fibers. A carding machine smoothes the fibers by brushing the wool over a series of rolling drums covered in pointed teeth. The drums are different sizes and rotate at different speeds, so as the wool progresses its fibers are aligned into a fine web.
The Woolen Process
Shorter wool fibers are used to make woolen yarn, which makes a rough, hairy fabric. After carding, the wool is gently twisted into ropes, ready for spinning into woolen yarn.
The Worsted Process: Combing
Finer, longer wool fibers are used to make worsted yarn, which makes a smooth, soft fabric. The carded wool is combed and drawn by passing over a series of tines to remove shorter fibers and comb long ones parallel, forming a long continuous rope called a sliver.
Spinning
Woolen and worsted wool are both processed by machines that draw out the ends of the fibers and spin them together by twisting at high speeds. The yarn can be spun into different thicknesses and strengths by varying the tension and direction of the twisting motion.
Weaving
The yarn is woven into fabric on looms, computerized machines that work at high speeds to interlace horizontal and vertical sets of threads, forming a flat cloth. A set of parallel warp (vertical) threads are held taut by the loom while weft (horizontal) threads are held in a shuttle. The loom lifts the warp threads up and down in sequence, creating a space between them that the shuttle passes through at high speed; several shuttles can be used simultaneously. This action weaves the two sets of threads together at right angles and creates fabric.
Different patterns are created by lifting the warp threads in different sequences and by using different colored yarns. Types of fabric made from wool include broadcloth, gabardine, herringbone, houndstooth and tweed.
Dyeing and Finishing
Wool can be dyed before carding or after being spun into yarn, or the finished fabric can be dyed. Fabric is treated with heat, moisture and friction to tighten the weave and shrink the fabric. To make the fabric fleecy, it is brushed to raise the nap, giving a fluffy finish. Chemical finishes can be applied to make the fabric washable by coating it with a resin film.
Related Articles
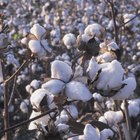
How Is Cotton Made?
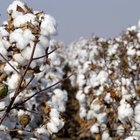
Types of Cotton Fabric
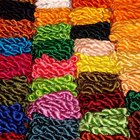
How Is Silk Made Into Fabric?
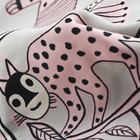
What Is Berber Fleece?
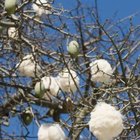
List of Plants Used for Clothing

How Is Cotton Made Into Fabric?
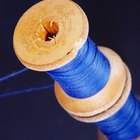
What Is a Synthetic Polyester Fabric?
What Is the Difference Between Acrylic ...
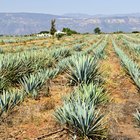
The Definition of Agave Fiber
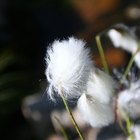
Define Cotton Silk Fabric
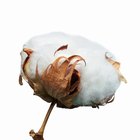
Ring Spun Cotton vs. Combed Cotton

What Is Superfine Wool?
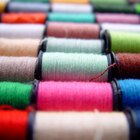
The Disadvantages of Polyester Cotton

Fabrics That Haute Couture Designers Use
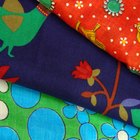
What Is Arnel Vintage Material Fabric?
How Is Poly Cotton Made?
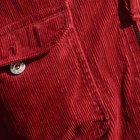
What Is the Difference Between Denim & ...
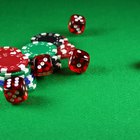
Different Types of Flannel Fabrics
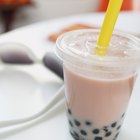
Differences Between Tapioca Starch and ...
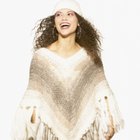
Properties of Cashmere Yarn
Writer Bio
Joanne Thomas has worked as a writer and editor for print and online publications since 2004. Her writing specialties include relationships, entertainment and food, and she has penned pieces about subjects from social media tools for Adobe to artists’ biographies for StubHub. Thomas has also written for such names as Disney, Hyundai, Michelob and USA Today, among others. She resides in California and holds a bachelor’s degree in politics from the University of Bristol, U.K.